奇石乐为施耐德电气的创新注塑成型提供过程监控支持
智能成型,一直是注塑数字化的重要组成部分之一。随着塑料零部件质量的要求越来越高,智能成型正在被越来越多的成型厂商所接受并使用。它以独特的可视化功能,简洁明了地展示了不可见的四大工艺变量之间的变化关系,为新工艺的建立及量产工艺的优化提供了直接有效的科学数据依据,科学注塑法和智能成型的珠联璧合,为合格、稳定的质量提供了强有力的保障。
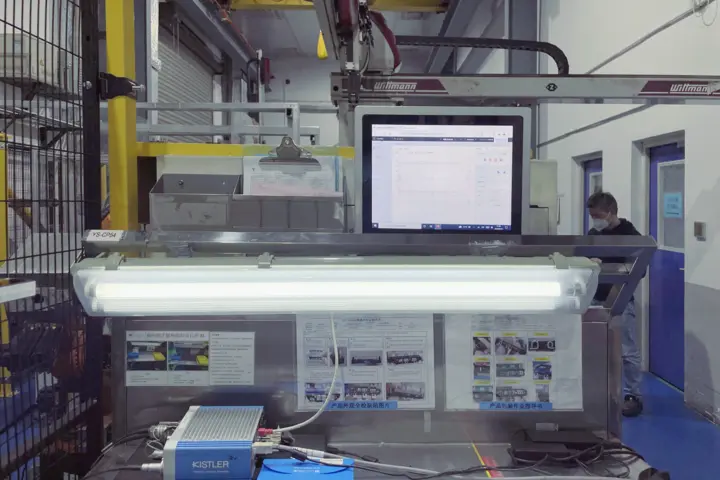
实时监控:改进的关键
智能成型,既是工业4.0时代数字化生产在注塑行业的独特诠释,又为“绿色减碳”提供数据支持和方向,同时还为制造商集中关注的“可持续发展”目标拓宽了通道。无论是汽车工业,电子3C行业,还是通用电气领域,各行各业的工程师需要凭借有效且快捷的方法,在每天不断变化的模具、材料、设备组合中找寻属于当下成型质量控制的最优解,发现影响质量的关键参数并及时做出调整。在诸多的成功典例中,就有着来自全球电气巨头、法国施耐德电气(Schneider Electric)的高级工程师、模具专家龙顺茂在该企业低压配电产品的Minitop Hammer部件生产过程中,依靠系统成型理论,配合来自瑞士奇石乐智能注塑方案,有效实现了注塑数字化的创新,生产能耗的降低,以及产品良率的提升。
Minitop Hammer因其需求量大、载荷要求高、尺寸严苛的特点,在施耐德低压电气诸多零部件中尤为重要。另一方面,于意大利、波兰、印度、中国等多个区域的异地生产使得该部件的质量同步率标准非同一般。作为精密塑料成型结构件,同时也是支撑着整个开关产品性能和耐久性能的核心部件之一,Minitop Hammer在强度、尺寸和使用寿命等诸多质量要求上皆有着较高的标准。为满足以上应用要求,施耐德工程师在诸多材料中选择了来自Sabic(沙特基础工业公司,Saudi Basic Industries Corporation)的PA66聚酰胺玻纤材料,其玻纤长度达到了12mm,玻纤含量更是高达60%,为本就不易的质量管控增添难题。
Dimension测试品 | 要求成品尺寸的一致性 |
DSC测试 | 确认零件的结晶度(Degree of Crystallinity),一定程度上可以反映材料性能的表征,要求高于95% |
VN测试 | 成品后材料的粘度数(Viscosity),确认成型过程是否合理,材料在成型过程中是否出现过度降解现象,要求粘度变化<10% |
X射线测试 | 了解成型后的材料上是否存在孔隙和空洞 |
力学测试 | 对卡扣等动作结构进行包含夹紧力、脱扣力以及弯曲力的测试 |
项目开始之前,具备丰富注塑理论和经验的龙工选择采用系统成型理论结合奇石乐智能注塑监控技术的解决方案来控制产品制程。具体方案包括在模具内总共布置了4个6182D型腔压力传感器和2个6195B温度传感器,结合ComoNeo过程监测系统,可输出直接反映二者与成型过程各阶段时间点的实时曲线,做到100%可视化。
在前期的技术评估中,因考虑到后续量产的经济性,模具设计选择了潜浇口。基于原料因素,可预见的是,这将影响整个成型过程中材料粘度一致性。从现在ComoNeo获取的数据来看,这也验证了前期的技术评估。最理想的情况肯定是牢牢控制在10%以下且数值波动范围小,但实际我们获取的测试数据是6%-18%,非常不稳定,这就是难点。注塑工艺上,塑料粘度数值可以反映出材料降解与否。在这个零部件的标准质量定义中,10%以内的粘度数值为合格,10%-20%为待评估,20%以上将被视作废品处理。
龙顺茂,施耐德电气GSC China KIP technology leader
从压力曲线上不难发现,当直接使用12mm、原始长度的材料颗粒来加工时,一腔四模的实时型腔压力曲线“如同起床时凌乱的发丝”,四根线的压力峰值(补缩结束时模内压力的特征点)参差不齐,彼此毫无重合的轨迹。但在其他参数不变的情况下,仅更换短玻纤材料,工艺稳定性就得到大幅度提升。
经此验证,更加确定是潜浇口和长玻纤的不匹配导致了浇口附近的熔体流动不畅或者堵塞;这些曲线还直观地显示了多型腔之间的材料充填差异,协助优化多腔之间的填充平衡。不仅如此,ComoNeo预测性的趋势保护功能协助了工程师及时发现长时间生产导致的浇口磨损+排气结构排气不畅等问题。
为了能够尽可能完善地监控成型相关的关键工艺参数,控制成型制程的稳定性, 工程师充分利用了ComoNeo的智能化功能。包括:
- 将ComoNeo采集的模内温度信号输出给模温机,实现了精准监控和控制模具温度的作用;
- 将ComoNeo识别的型腔填充完成信号发送给注塑机,以控制注塑机的V/P切换并达到稳定填充的作用
- 将ComoNeo系统识别的次品信号发送给分拣设备,确保不良品不会流出到下一生产环节
- 将系统异常信号发送给注塑机,当整个注塑系统出现异常时,及时将异常信号发出,避免大量不良品产生,这些异常包括但不限于浇口磨损,螺杆磨损,模温异常等
经调整并规定各项质量标准后,该部件的成型废品率从13%降低到了8%。“可惜的是,如果可以搭配热流道,结合奇石乐ComoNeo的热流道控制技术,废品率有机会进一步降到1%。“对此龙工深表遗憾。
智能成型是一个始于动态测量的注塑成型闭环控制交互体系,而智能化的自动调节,即工艺自适应能力是施耐德电气,也是奇石乐致力追求的目标。它能为稳定的产品品质保驾护航而不需人工干预。目前,第3个智能层面是双方专家团队正在努力的目标,涉及到温度(特别是多热嘴)、螺杆位置(特别是VP点)、压力(特别是型腔压力)的自动调节,除了ComoNeo软件功能外,还需相应的硬件设备支持。
施耐德和奇石乐在欧洲地区的合作可以追溯到法国总部在注塑项目上内部推广使用的智能注塑解决方案,其中包含来自奇石乐的传感器和放大器设备。而在中国,双方正式的技术交流起步于2020年下半年。2年来,多个生产项目上的合作让施耐德电气模具部门对于奇石乐产品,尤其是ComoNeo系统及奇石乐注塑团队有着很高的评价, “我们通过大量的测试和数据报告比较了市面上的各类同类产品。最后还是做出了法国总部一样的选择。如今奇石乐的表现也让我们更加认可这个多年的合作伙伴。值得一提的是,奇石乐中国的工程师在专业技术上给我们留下了深刻印象,常在实际问题的解决思路上提供建设性意见。” 来自施耐德电气模具团队的肯定无疑将会使得双方的合作更加深入,在未来共同创造更多的双赢局面!