Gegründet 1836, gehört das Unternehmen Schneider Electric SE mit Hauptsitz in Rueil-Malmaison (Frankreich) zu den „Fortune Global 500“. Die multinationale Gruppe verfügt über die Hauptgeschäftsbereiche intelligente Energieverteilung, elektrische Fassungen und Steuerungskomponenten für die Industrieautomation. Mit mehr als 120.000 Mitarbeitenden weltweit erreichte Schneider Electric 2022 einen Umsatz von etwa 34 Mrd. Euro, verteilt auf über 100 Standorte und Regionen. In zwei wichtigen Industrien – Energieversorgung und Industrieautomatisierung – fiel das Ergebnis mit 10 Prozent Zuwachs besonders stark aus. In China tätig seit 1987, betreibt Schneider Electric dort vier Forschungs- und Entwicklungszentren sowie 23 Werke mit landesweit etwa 17.000 Mitarbeitenden. Das Unternehmen übernimmt außerdem eine tragende Rolle in den Initiativen „Digitale Innovation“ und „Grüne Dekarbonisierung“, die von der Chinesischen Regierung auf allen Ebenen vorangetrieben werden.
Kistler unterstützt Schneider Electric mit Prozessüberwachung für hochentwickeltes Spritzgießen
Für die Qualitätssicherung und Datenvisualisierung wurden vier Werkzeuginnendrucksensoren 6182D und zwei Temperatursensoren 6195B von Kistler im Werkzeug installiert. Der 6182D ist ein piezoelektrischer Miniatur-Druckaufnehmer mit einem Durchmesser von 2,5 mm, einem Messbereich bis zu 2000 bar und einer flexiblen Anschlussoption (Einzelkabel oder Distanzhülse).
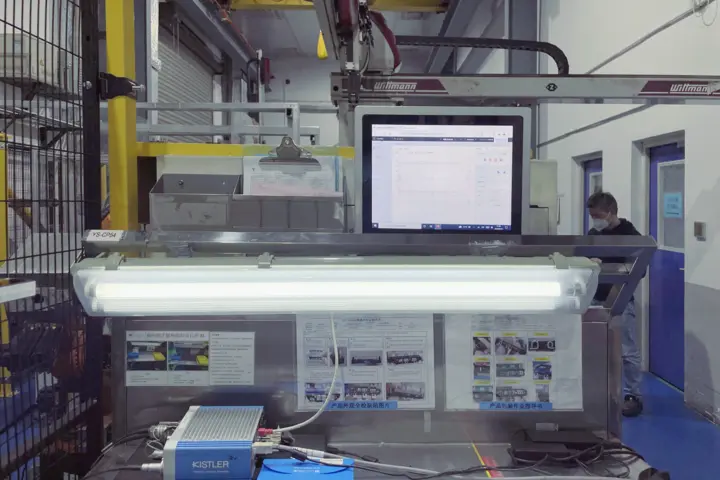
Echtzeit-Überwachung: der Schlüssel zur Verbesserung
Schneider Electric strebt danach, den Ansatz des intelligenten Spritzgießens in sämtlichen Fertigungsprozessen weltweit zu verwirklichen (wie in der Grafik zu sehen). Um dieses Ziel zu erreichen, wird Technologie von Kistler im Unternehmen Schneider aktiv gefördert – verfügbar in Form eines Komplettpakets, das Werkzeuginnendrucksensoren und passende Ladungsverstärker enthält. So haben Schneider Electric China und Kistler ihre Zusammenarbeit in der zweiten Hälfte des Jahres 2020 begonnen, nicht lange nach dem ersten Kontakt der beiden Unternehmen. Die Abteilung Spritzgießen von Electric China profitiert zunehmend von dieser Partnerschaft, denn sie erhält Unterstützung von Ingenieuren von Kistler China in Form von technologischem Know-how und konstruktiven Vorschlägen. Auf diese Weise wurden bereits viele praktische Probleme gemeinsam gelöst.
Long Shunmao, KIP Technology Leader bei Schneider Electric GSC China und Experte für das Spritzgießen, ist verantwortlich für die Produktion des Minitop, einer Komponente im Niedrigvolt-Elektroverteiler-Portfolio des Unternehmens. Um höchste Produktqualität und Prozesssicherheit zu sichern, kombinierte Long einen wissenschaftlichen Ansatz mit Werkzeuginnendruck- und Temperatursensoren sowie einem Prozessüberwachungssystem von Kistler. Das Verfahren zielt besonders darauf ab, vier im Spritzgießprozess nicht direkt beobachtbare Variablen und ihre Schwankungen zu verstehen und zu steuern: Einspritzgeschwindigkeit, Schmelzetemperatur, Schmelzedruck sowie Kühltemperatur und -zeit.
„Die Minitop Produkte müssen strenge Qualitätskriterien erfüllen, zum Beispiel hinsichtlich Stärke, Dimensionen und Lebensdauer“, berichtet Long.
„Deshalb hatten wir in der anfänglichen technologischen Evaluation seitliche Anschnitte für das Werkzeugdesign und Polyamid 66 (PA66) ausgewählt – ein Material mit einem Glasfaseranteil von 60 Prozent und 12 mm langen Fasern. Doch dann mussten wir einen Weg finden, um alles zum Laufen zu kriegen – und Kistler hat uns die richtige Lösung geliefert, um die Stabilität über den gesamten Prozess zu gewährleisten.“
Long Shunmao, KIP Technology Leader bei Schneider Electric GSC China
Höhere Produktqualität, weniger Ausschuss
Für die Qualitätssicherung und Datenvisualisierung wurden vier Werkzeuginnendrucksensoren 6182D und zwei Temperatursensoren 6195B von Kistler im Werkzeug installiert. Der 6182D ist ein piezoelektrischer Miniatur-Druckaufnehmer mit einem Durchmesser von 2,5 mm, einem Messbereich bis zu 2000 bar und einer flexiblen Anschlussoption (Einzelkabel oder Distanzhülse).
Die von den Druck- und Temperatursensoren zur Verfügung gestellten Daten werden visualisiert und bewertet vom Prozessüberwachungssystem ComoNeo, das Echtzeitkurven über den gesamtem Spritzgießprozess hinweg bereitstellt. Wie bei der Kombination von Tunnelanschnitten mit einem Material mit langen Glasfasern zu erwarten war, ergaben sich im Produktionsprozess zusätzliche Herausforderungen, so dass die gefertigten Teile Qualitätsmängel in verschiedenen Aspekten wie Abmessungen oder Viskosität aufwiesen.
In Übereinstimmung damit zeigten die Druckkurven in ComoNeo ein Missverhältnis zwischen den Tunnelanschnitten und den langen Glasfasern auf, so dass der Schmelzefluss in der Nähe der Anschnitte oft behindert oder versperrt war. ComoNeo erkannte außerdem ungleiche Füllstände zwischen den Kavitäten. Long berichtet: „Zuerst haben wir die Hauptursache des Problems ermittelt; sobald wir die Qualitätsstandards für jeden Prozess angepasst und definiert hatten, konnten wir die die Fertigungsleistung beträchtlich steigern.“ Die folgende Übersicht zeigt, welche Features des Prozessüberwachungssystems von Kistler zur Qualitätssicherung und Optimierung angewendet wurden:
- Überwachung und Steuerung der Werkzeugtemperatur mit Hilfe von Sensorsignalen
- Steuerung der V/P-Umschaltung, um eine stabile Füllung zu garantieren (ComoNeoSWITCH)
- Separierung von Ausschuss auf Basis festgelegter Qualitätskriterien
- Stopp der Produktion im Fall abnormer Bedingungen (z.B. Abnutzung, hohe Temperatur etc.)
Auf dem Weg zur automatisierten Optimierung
Die ganzheitliche Prozessoptimierung reduzierte die Ausschussrate in dieser Anwendung – von 13 auf acht Prozent insgesamt. Die fertigen Teile werden zusätzliche Röntgen- und Belastungstests unterzogen (aufspannen, auslösen, biegen), um eine einheitliche Qualität zu erreichen. Und Long hat bereits die nächsten Schritte vor Augen: „Theoretisch könnte die Ausschussrate für diese herausfordernde Komponente auf etwa 1 Prozent gesenkt werden – vor allem, wenn wir zusätzlich das Feature ComoNeoMULTIFLOW einsetzen würden.“ Diese Softwareerweiterung für ComoNeo erlaubt eine Temperatur-basierte Balancierung des Heißkanals und kann so Material- und Prozessschwankungen automatisch kompensieren.
Das übergeordnete Ziel von Schneider GSC China ist es, ein Steuerungssystem mit geschlossenem Regelkreis auf Basis dynamischer Messtechnik für das Spritzgießen zu etablieren. Das schließt eine intelligente und automatische Regelung in einem selbstlernenden Prozess ein, der eine stabile Produktqualität ohne menschliche Eingriffe garantiert. Ein solches Resultat würde Ebene 3 des intelligenten Spritzgießens entsprechen, basierend auf automatischer Temperaturanpassung (für multiple Einspritzdüsen), Schraubenposition (V/P-Umschaltpunkt) und Werkzeuginnendruck.
Long Shunmao resümiert: „Spritzgießingenieure brauchen effiziente Methoden, um vielfältige, sich immer wieder ändernde Kombinationen von Werkzeugen, Materialien und Ausrüstung zu meistern. Mit Hilfe von intelligenten Spritzgießlösungen und professioneller Beratung von Kistler ist es dem Fertigungsteam von Schneider Electric gelungen, drei wichtige Ziele zu erreichen: innovative Digitalisierung des Spritzgießprozesses, weniger Energieverbrauch und höhere Produktivität.“