Zylinderdrucksensoren von Kistler tragen zur Emissionsreduktion in Großmotoren bei
Mit Messtechnik von Kistler lassen sich Verbrennungsprozesse in großen Schiffsmotoren nachhaltig optimieren: Emissionen und Betriebskosten sinken, die Lebensdauer erhöht sich. Die Weiterentwicklung der Zylinderdrucksensoren für Großmotoren steht im Zeichen alternativer und flexibel nutzbarer Kraftstoffe (Multi-Fuel). – Außerdem trägt Kistler mit hochspezialisierten Testlösungen zur Evolution des Schiffbaus bei, zum Beispiel bei LNG-Tankern.
Die International Maritime Organization (IMO) hat deshalb eine Reduzierung der Treibhausgasemissionen auf Netto-Null um das Jahr 2050 gefordert. Einige große Reedereien verfolgen jedoch ein deutlich ehrgeizigeres Ziel und wollen bereits bis 2040 klimaneutral fahren. Um ein solches Ziel zu erreichen, ist die schnelle Einführung alternativer Kraftstoffe geboten, zum Beispiel „grünes“ Ammoniak oder Methanol, das mit Hilfe erneuerbarer Energien produziert wurde.
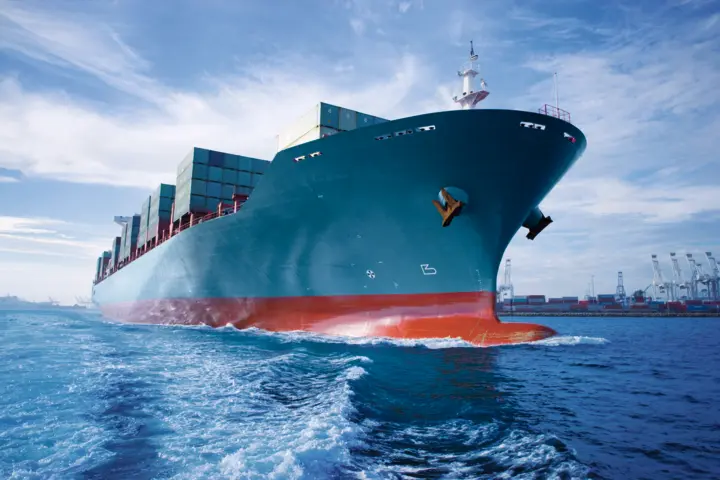
Kontinuierliche Überwachung von Großmotoren senkt CO2-Ausstoß
Messtechnik-Lösungen von Kistler tragen bereits heute zu erheblichen Einsparungen und zur Vermeidung von Emissionen bei. Kistler hat in den vergangenen zwölf Jahren Tausende von Zylinderdrucksensoren in Serie geliefert, um Großmotoren in Schiffen, die mit Öl oder Erdgas fahren, kontinuierlich zu überwachen und deren Leistung und Ressourceneffizienz verbessern. Als Teil von Systemen mit geschlossenem Regelkreis (CLCC: Closed Loop Combustion Control), die in enger Zusammenarbeit mit Motorherstellern entwickelt wurden, helfen die Sensoren von Kistler dabei, bis zu zwei Prozent Treibstoff einzusparen, Stickoxid-Emissionen (NOx) zu reduzieren und die Motoren vorausschauend zu warten.
Ein Rechenbeispiel aus einer realen Anwendung verdeutlicht das enorme Potenzial der CLCC-Technologie: So verbraucht ein moderner Großmotor mit 112.000 PS bei Volllast etwa 325 Tonnen Treibstoff pro Tag. Durch die Installation eines CLCC-Systems mit Zylinderdrucksensoren von Kistler reduziert sich der Verbrauch um 1,8 Prozent (entspricht ca. 3 Gramm pro Kilowattstunde). Umgerechnet auf die CO2-Emissionen, ergibt sich eine Ersparnis von mehr als 18 Tonnen Treibhausgas pro Tag. In einem Jahr bedeutet das nur für diesen Motor die Vermeidung von mehreren Tausend Tonnen CO2. Nicht zuletzt vermindern sich natürlich auch die Treibstoffkosten – um mehr als 2.000 Euro täglich, so dass sich Investitionen in CLCC-Systeme mit Zylinderdrucksensoren von Kistler schnell amortisieren.
Evolution in Richtung alternative Kraftstoffe und Multi-Fuel
Kistler entwickelt seine Zylinderdrucksensoren für Großmotoren kontinuierlich weiter, sowohl für Zweitakt- als auch Viertaktaggregate. Die piezoelektrischen Druckaufnehmer zeichnen sich vor allem durch ihre Genauigkeit, Robustheit und lange Lebensdauer aus. Sie messen über viele Jahre gleichbleibend stabil in Großmotoren – auch im Dual- und Multi-Fuel-Betrieb – und weisen daher sehr niedrige Gesamtbetriebskosten (TCO: Total Cost of Ownership) auf. Dual- und Multi-Fuel, also der Betrieb mit mehreren unterschiedlichen Kraftstoffen, ist auch ein wichtiger Faktor für stationäre Großkraftwerke, die künftig mit grünem Wasserstoff betrieben und vor allem eine Rolle als Stabilisatoren im mehrheitlich mit erneuerbaren Energien gespeisten Stromnetz spielen werden.
In enger Zusammenarbeit mit führenden Motorherstellern entstehen so Lösungen wie der Sensor 6635A1 von Kistler, der seit 2018 im Serieneinsatz ist. Dank innovativer Features wie dem hochempfindlichen PiezoStar-Kristall, der optimierten Membran und der besonders robusten Signalübertragung eignet sich der Zylinderdrucksensor besonders für den Multi-Fuel-Betrieb. Dank aufwendigen Langzeittests verfügt der 6635A1 über eine hohe Lebensdauer bei gleichbleibend stabilen Messergebnissen im CLCC-Betrieb. Auch wenn im Moment noch nicht abzusehen ist, welcher Treibstoff sich in Zukunft durchsetzen wird – etwa Ammoniak, Methanol oder Biodiesel – Kistler steht bereit, um mit entsprechend weiterentwickelten Sensoren die Evolution von Großmotoren voranzutreiben.
Hydrodynamik-Testlösungen für die Seeschifffahrt
Neben der Motorenoptimierung unterstützt Kistler die weltweite Seeschifffahrt auch mit hydrodynamischen Testlösungen. Bevor ein Schiff betriebsbereit ist, werden unzählige Tests durchgeführt: In sogenannten Schlepptanks kommen zunächst Schiffsmodelle zum Einsatz, um die hydrodynamischen Eigenschaften zu optimieren. Und bei der Entwicklung des Antriebs kommt es insbesondere darauf an, Kavitation und unerwünschte Schwingungen zu vermeiden. Bei einer Reihe weiterer spezieller Tests spielen die piezoelektrischen Sensoren von Kistler ihre Stärken aus – sind sie doch in der Lage, kurzzeitige, das heißt sich im Sekundenbereich und darunter abspielende Kraft- und Druckveränderungen besonders genau zu messen.
Eine weitere spezielle Anwendung ist das sogenannte Sloshing: Dabei geht es darum, die Bewegungen des in modernen LNG-Tankern transportierten flüssigen Erdgases zu kontrollieren. Durch die Schiffsbewegungen und den hohen Druck in den Tanks mit ständigen Aggregatzustandsänderungen kann es zu Resonanzen und Kavitätenbildung kommen, die die Sicherheit der Tanker gefährden. Um solche Eventualitäten auszuschließen und die Konstruktion insgesamt zu optimieren, werden an Forschungsinstituten, zum Beispiel in den Niederlanden, umfangreiche Untersuchungen durchgeführt, bei denen Lösungen von Kistler eine entscheidende Rolle spielen.