2-axis force and reaction torque transducer, Fz max ±10 kN, Mz max ±25 Nm / 9345B
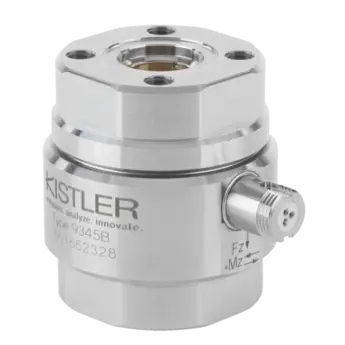
9345B
18007692
- Preloaded and calibrated force-torque sensor, ready to measure immediately
- Calibrated ranges: Fz: 0 … +1 kN, 0 … +10 kN; Mz: 0 … ±2.5 Nm, 0 … ±25 Nm
- Sensitivity: Fz: ≈ –3,7 pC/N, Mz: ≈ –190 pC/Nm
- Dimensions: DxH (mm) 36x42
Upon request
On request
Measuring ranges
Minimum measuring range [kN]
-10 kNMaximum measuring range [kN]
10 kNThis piezoelectric 2-axis force-torque transducer is suitable for measuring a tensile or compression force Fz and a torque Mz acting on the sensor. The high resolution allows measurement of the slightest dynamic changes in large forces and torques at non-rotating shafts. Pressure and shear sensitive quartz disks are integrated under high preload between a hollow preload screw and a nut de signed as the sensor case. Because of the extremely high rigidity of the sensor elements, the components Fz and Mz are measured practically without change of stroke or angle. The force and torque-proportional charge signal is picked up by electrodes and fed via a shielded cable to the charge amplifier. The latter converts the charge signals into proportional output voltages, which can be recorded and evaluated.
Loading
Loading