Kistler accelerometer features 27 percent lower noise threshold
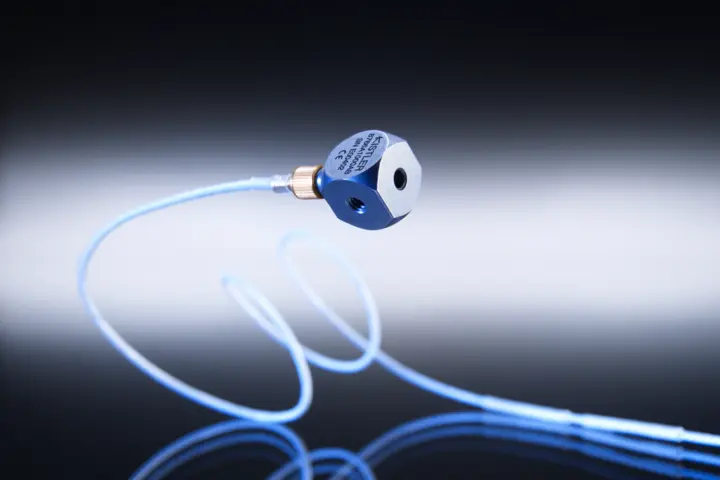
Measuring micro-vibrations is necessary in many engineering applications: accurate GPS data depends on stable space crafts and satellites just like automobile developers need NVH testing (noise, vibration and harshness) to optimize vehicle performance, durability and reliability. Because micro-vibrations occur in the micro g range, a highly sensitive measuring chain with very low noise is required for such applications.
The IEPE (Integrated Electronics Piezoelectric) triaxial accelerometer 8763B050 is the most common Kistler sensor used for these measurements and permits vibration monitoring in three mutually perpendicular axes. The measuring threshold determines the smallest possible level of vibrations that can be reliably picked up by the sensor. Thanks to improved electronics, the 8763B050 has a threshold of only 0.00029 g, compared to previously 0.0004 g.
Type 8763B sensors provide wide frequency response in each orthogonal axis, making it well suited for dynamic vibration measurements, especially on lightweight structures. Other features include the sensors’ lightweight hermetic Titanium housing and high immunity to base strain thanks to shear element technology. Additionally, a miniature 4-pin ceramic-insulated connector provides long-term stability over a large operating-temperature range. An integral silicone cable variant is available for application of underwater vibration testing at up to 10 bars. Sensors of the 8763B family can be installed on test objects by either adhesive mounting or by flexible studs thanks to three 5–40 threaded holes. This allows for fully utilizing each mounting side of the cube design and provides reliable mounting for the calibration of each axis.