The dimensions are exactly right
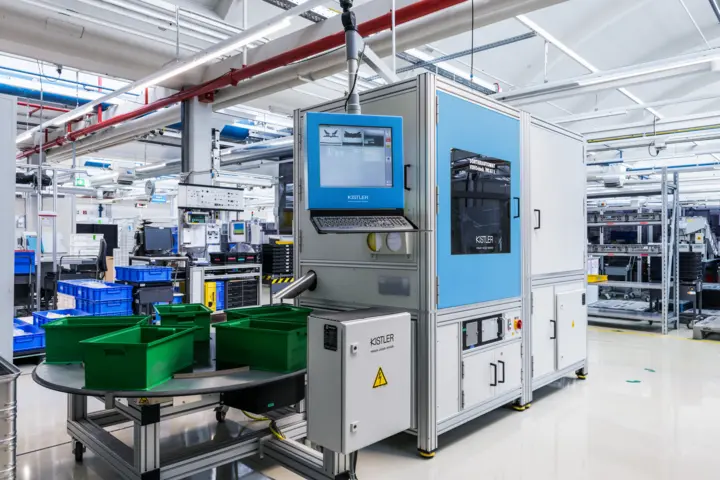
Virtually no complaints
Electric shavers are complex products that can consist of 200 to 300 highly intricate individual parts, depending on the type. To ensure that quality is the defining aspect of the customer experience, every one of these parts has to be perfect. Thanks to automatic testing and sorting systems by Vester, the company can guarantee that the parts in its end products meet very high quality and functionality standards. Comprehensive quality monitoring during and after the production process has significantly reduced the internal complaint rate. End-to-end quality monitoring has had an equally positive impact on warranty cases: here too, the rate has fallen substantially.
Precision - even with high throughput rates
Three Vester automatic testing and sorting systems are currently operating on the company's plastic production lines, and a feasibility study for a fourth unit is already in progress. Eight more Vester systems are installed in the automated turning shop. To ensure excellent product performance, these systems test numerous items including outsourced metal parts such as the pins built into shaver heads and electric toothbrushes.
The testing rates and speeds required for plastic part production are exceptionally high. Correct positioning of individual parts as they are fed into the test line is essential to guarantee the necessary precision and to ensure high throughput rates. The aim here is to exclude parallax errors that occur because the camera's angle of view is distorted.
"Our testing systems meet the demanding requirements regarding the complex geometry and high volumes. They helped to improve the quality of each individual part as well as of the complete device. Therefore, the customer owns an efficient solution."
Samuel Ganzhorn, Application Specialist
Systems for universal use
At present, several million plastic parts are tested and automatically sorted in the plant each year. Two VVC 120 systems (based on the inclined-plane principle) and one VVC 811 system (with a continuously rotating glass plate) supply answers to questions such as these: Are the parts deformed? Is there any flash formation? Do dimensions adequately meet the specification? Testing focuses on particularly critical parts that are crucial for function and performance.
This electrical appliance manufacturer sees two factors as decisive: the flexibility of Vester's systems, and their high performance. With a suitable setup, multiple features can be tested on one part. But that is not all: different components can also be tested on one system with minimum effort. Customers benefit from Vester's support with application changes: they can choose to have their camera and feed systems reconfigured on their own site or, for major conversions and retrofits, the work can be carried out at Vester's plant.
Thanks to its close collaboration with Vester, the manufacturer is able to meet the demanding requirements set by its parent company. Standard automatic testing systems always need to be adapted for each and every application, so their suitability for testing highly intricate plastic parts is limited. Vester's solutions take account of complex geometry, advanced testing requirements and high volumes: as well as boosting cost efficiency, they help to enhance product quality. The successful results of quality assurance with test automation by Vester are clear: models from this high-quality German manufacturer regularly occupy the top places in independent consumer tests.
Test results: the basis for process optimization
This manufacturer of shavers and epilators can look back on many years' successful experience of using Vester's automated test systems for metal parts. Vester continuously develops its solutions, with the focus on individual customer requirements. For this customer, inhouse testing is another advantage that should not be underestimated. Because users acquire know-how about specific repeated deviations on the spot, they can draw conclusions about the injection molding process and initiate steps to optimize it. With the help of Vester's systems, the customer can (for example) easily check which cavity was used for a defective part. By reading out the relevant identification code, users can track down the specific problem points in the process.
High-performance process monitoring is a critical factor in ongoing optimization and automation: it ensures that products such as shavers and epilators will convince and inspire end customers, now and in the future - and the manufacturer can continue to predict lifetimes of up to seven years. By partnering with Vester, this customer gains access to technologically mature solutions that deliver highly efficient quality testing for plastic and metal parts. Vester thus plays a key part in delivering a customer experience that will stand the test of time.