The story began when three friends – students at the same high school – discovered their shared passion for space and spaceflight. Then in November 2018 – soon after Jérémy Marciarq, Julie Böhning, and Simon Both commenced their studies at École Polytechnique Fédérale de Lausanne (EPFL) – they started experimenting with small 3D-printed models. They were inspired by SpaceX and worldwide advances in reusable VTVL rocket technology (vertical take-off, vertical landing).
Gruyère Space Program masters vibration and thrust testing for its VTVL rocket hopper with Kistler
The Gruyère Space Program (GSP), founded by three Swiss students, has achieved its goal of building Europe’s first free-flying rocket hopper. Named Colibri, GSP’s reusable liquid rocket hopper launches vertically, navigates freely, and then lands safely on the pad. Supported by Kistler measurement technology, the GSP team has completed rocket thrust testing and vibration monitoring to optimize propulsion and control algorithms – and now, the world’s first student-built rocket hopper has accomplished its mission with flying colors!
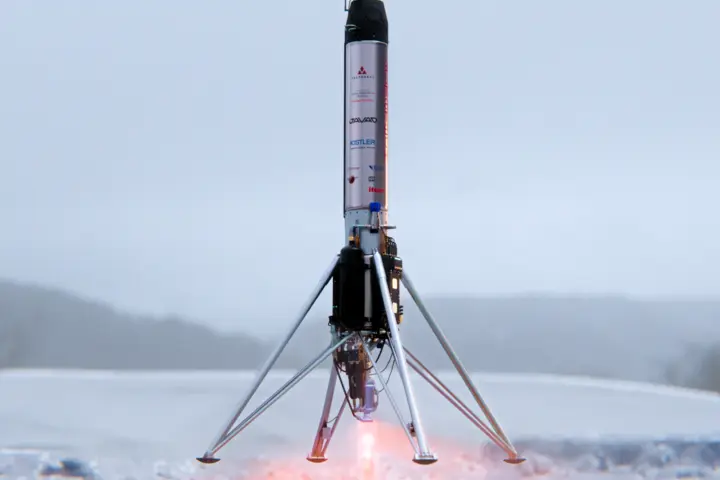
When the three students set up an association to develop a VTVL rocket hopper, they named it ‘Gruyère Space Program’ after their home region in western Switzerland – also, of course, famed for its cheese. Two more EPFL students joined them to create a core team of five members who stayed on board throughout the project. Operating from a barn in Lessoc in the heart of the Gruyère region, GSP soon professionalized and attracted over 60 sponsors, including the Kistler Group as a Gold Partner.
Julie Böhning, one of the three co-founders, studied robotic engineering at EPFL and went on to become CEO of PAVE Space SA, the company spun off from GSP. She recounts: “We got to know measurement technology from Kistler during our internships in Germany, and we met up with them again later on at the Space Tech Expo. So we knew they are the gold standard for space testing, and we were thrilled when they came on board as a sponsor.”
Rocket engine testing: critical support with thrust testing and vibration monitoring
Colibri, the reusable VTVL rocket demonstrator, stands 2.45 meters tall and is powered by a bipropellant liquid rocket engine that uses nitrous oxide (N2O) and isopropanol (IPA) as propellants. The engine generates up to 1.25 kN of thrust and carries a 3 kg payload. During testing, the Gruyère Space Program utilized three different sensors from Kistler:
- Piezoelectric press force load cell 9333A: used for thrust testing and characterization, mounted directly in front of the injector head with a measuring range (Fz) of 0 to 50 kN.
- Piezoelectric pressure sensor 601CAA: installed in a small channel between injector head and the combustion chamber, this sensor measures pressures up to 250 bar and operates in a temperature range of –196°C to 350°C. The 601CAA provided critical data for pressure monitoring and optimization of the rocket thrust-to-combustion chamber pressure ratio.
- IEPE (Integrated Electronics Piezo-Electric) triaxial accelerometer 8763B: the sensor was used for vibration monitoring and analysis.
Jérémy Marciacq explains: “We experimented with various mounting points: ultimately, the accelerometer delivered the most representative data when it was attached to our INS (Inertial Navigation System). These measurements assisted in characterizing the propulsion system and fine-tuning the flight control.” Julie Böhning adds: “Without vibration compensation, the hopper initially danced uncontrollably. It was only after we optimized the control algorithms based on the acceleration measurement data that it was able to maintain a stable position.”
Europe’s first free-flying rocket hopper: flight program accomplished successfully!
By October 2024, the Gruyère Space Program team had grown to 15 members, with participants joining from across Europe. Colibri completed 53 flights at varying altitudes, performed special maneuvers, and carried different payloads – ending with a safe landing every time. On completing this free-flight campaign, GSP became the first student project to design and launch a reusable VTVL rocket. Julie Böhning reflects: “The transfer from theory to practice really was a huge leap for everyone. Regarding measurement technology, Ayoub Bounouara from Kistler gave us tremendous support. It isn’t at all easy to obtain reliable data during rocket engine and thrust testing, but Kistler’s technology is highly accurate – and in the end, it proved even more helpful than we expected.”
Kistler’s sponsorship included the sensors themselves as well as a complete measuring chain featuring KiDAQ hardware and jBEAM software. KiDAQ is the universal data acquisition system that offers intuitive configuration and automatic synchronization for all connected sensors. Up to 13 modules plus a controller can be integrated in one flexible housing (portable, rack, or DIN rail), capturing more than 20 different signal types. “We had a really good experience with KiDAQ: it’s user-friendly, highly reliable, and more or less plug-and-play,” Jérémy Marciarq comments. “jBEAM also helped us with rapid measurement data processing, and with finding and filtering resonance frequencies to optimize our closed-loop simulation and rocket hopper control.” jBEAM is Kistler’s fast, powerful measurement data analysis software that supports data import from over 100 file formats. It offers versatile visualization, advanced analysis features, and automated reporting capabilities.
From VTVL rockets to space logistics: GSP evolves into PAVE Space
Following Gruyère Space Program's successful demonstration of the VTVL rocket hopper, members of the team who had now graduated from EPFL went on to found their own company: PAVE Space, located in Renens near Lausanne. Drawing on GSP’s expertise, PAVE Space is pioneering space logistics by leveraging its know-how in GNC (Guidance, Navigation, and Control) algorithms and propulsion technology to develop innovative docking solutions. “Refueling is critical, especially in Earth orbit”, Böhning explains. “Our technology can extend satellites’ lifespans and will support logistic, assembly, and maintenance of tomorrow’s large space infrastructure.”
After completing a first investor round, concrete goals are at the horizon: In 2027, PAVE Space is involved in a special satellite launch and will provide technologies for satellite approach and inspection. For 2030, PAVE Space is targeting a rendezvous with a TV satellite: their spacecraft will act as a second propulsion system to extend the life of assets already in space. Final words from Julie Böhning: “In this initial phase, we’re focusing on providing our software to clients – but as soon as we need to go back to hardware, we’ll be happy to work with Kistler again. Their technology was essential for rocket engine testing, thrust characterization, pressure and vibration monitoring – and our partnership also remains strong at the personal level.”