6-axis piezoelectric force-torque sensor (Fx, Fy, Fz, Mx, My, Mz, low profile version) / 9306A31
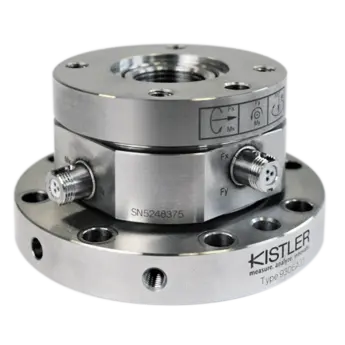
- 6-axis force-torque sensor, low profile with measuring ranges Fx, Fy: -1 ... 1 kN, Fz: -2 … 2 kN and Mx, My, Mz: -100 … 100 Nm
- Connection: 2 x V3 neg.
- Dimensions: DxH (mm) 83x45
Measuring ranges
This 6-axis force-torque sensor measures all forces and the corresponding moments on the three orthogonal axis. All forces and moments are captured as physical, piezoelectric signals and do not need to be calculated. The unique measurement setup of this multi-axis force-moment sensor allows an extremely small and compact design. Therefore concise models of 3-dimensional dynamic and quasistatic processes are possible even in narrow installations. Pretensioned piezoelectric 6-axis force-torque sensors with two mounting flanges. Measures forces and reaction torques in both tensile and compression directions. A force or reaction torque generates a proportional electrical charge. This is transferred by an electrode to the corresponding connector. The multi-axis force-torque sensor consists of large-area quartz discs and is therefore very rigid. The resulting high natural frequency is a prerequisite for highly dynamic force and torque measurements. The two 3-pole V3 neg. connectors are provided with an antitwist lock. One connector each for force and torque signals. After it has been correctly installed the 6-axis force-torque sensor is immediately ready for use without recalibration.