Shaft torque sensors, dual range torque transducers (measuring ranges 0.2 Nm to 5 kNm) / 4503B
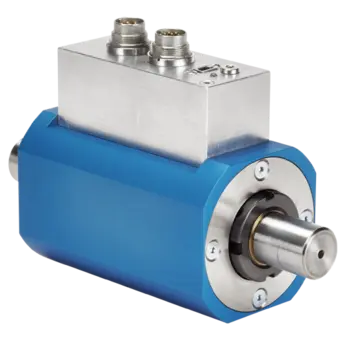
4503B
Main features / advantages
- Dual range sensor with two separately calibrated torque measuring ranges
- Analog and digital interfaces
- Well suited for static and dynamic measurements with a cut-off frequency (–3 dB) 10 kHz
- Very high accuracy thanks to linearity error including hysteresis of only 0.05 %
- Operational up to 50000 1/min
The dual torque transducer offers the advantage of freely scalable range switching, which allows highly accurate measurement of both the peak and particularly the operating torque. The shaft torque sensor offers an integrated high-resolution speed/angle measurement sensor up to 8192 pulses/revolution, freely scalable. Additionally, the rotational direction as well as an absolute zero point (Z-line) are available. Power is supplied and the measurement signals are transferred between the rotating shaft and the case without contact. In addition to suitable mounting of the shaft, low production tolerances and high-grade balancing, this is a further prerequisite for the high speed limit of up to 50 000 1/min achieved with the "H" version.
How is the accuracy class defined for torque shaft sensor/ torque transducer Type 4503B?
The accuracy class is a quality feature for force and torque transducers from Kistler. It is generally specified as a positive numerical value and is determined by the largest value of the specified relative influencing parameters.
The following parameters are decisive for the definition of the accuracy class of the torque shaft sensor/ torque transducer:
- Linearity including hysteresis
- Temperature influence on the zero signal (per 10 K)
- Temperature influence on the characteristic value (per 10 K)
- Repeatability
The accuracy class described here and specified in Kistler data sheets is not to be confused with the classification features according to the EN ISO 376 or DIN 51309 guidelines. Rather, this manufacturer's specification is used for the comparability of similar sensors, as a summarizing and greatly simplifying quality feature.
Do I really need a coupling to operate the Type 4503B torque sensor/ transducer?
Two full couplings (double flexible) recommended for the installation of the shaft torque sensor.
What is the advantage of a second measuring range for a Type 4503B dual-range torque measurement shaft sensor?
Kistler offers additional several types in this torque transducer family (4503B..., 4503BQ..., 4510B..., 4550A..., 4551A...) with a dual-range option.
This is for customers who require:
- A Reserve to the nominal range of the sensor
- High accuracy measuring also in the first 10% of the nominal range
- Full resolution of the output signal also in smaller ranges
In the following an example which explains the accuracy advantage in the extended range. Each measuring range is calculated the tolerance on full scale output.
Means in the example of a 100Nm sensor +/-0,05Nm and in the extended range +/-0,01Nm. In conclusion the accuracy in Nm is 5 times better in the extended range than in the first range when you measure <10% accuracy (non-linearity) requirements.
What are typical applications for the torque shaft transducer type 4503B?
The torque transducer can be used in following applications:
- In automotive and vehicle engineering Efficiency of electric motors or ripple test
- In the aviation and aerospace industry Efficiency of propeller or turbines in relation to thrust
- In pump testing Efficiency of the pump
- In the development and production of electric motors for determining characteristic maps
What is the maximum operating (rotational) speed of the Type 4503B torque shaft sensor?
- Low speed ranges up to 20 000 rpm
- High speed ranges up to 50 000 rpm
Does a double-flexible coupling make an exact alignment axle to the Type 4503B torque shaft sensor unnecessary?
Exact alignment must always be ensured to minimize the resulting negative influences on the measurement result and the service life of the bearings and the torque sensor.
How accurate is angular accuracy for a Type 4503B torque transducer with shaft with rotation angle option?
The angular accuracy of a Type 4503B torque transducer with shaft and rotation angle option is ±0.03°.
Is the bearing friction also measured with a Type 4503B torque shaft sensor?
No. The unique design of the smaller sizes is such that the bearing friction on the measuring side is not included in the measurement result.
How many pulses can be set for a Type 4503B torque shaft sensor with angle option?
Up to 8192 pulses can be set for the Type 4503B torque shaft sensor.